Lean (Sigma)
Nach dem Ende des Zweiten Weltkriegs half der Marshall-Plan Europa, wieder zügig auf die Beine zu kommen. Nach Japan gingen wesentlich weniger Geldmittel - aber General MacArthur konnte Edward Deming davon überzeugen, in Japan aktiv zu werden. Sein Credo: aktive Einbeziehung aller Mitarbeiter - Verantwortung auch auf die Arbeitsebene delegieren ("Empowerment") (Dr. Deming: The American Who Taught the Japanese About Quality von Rafael Aguayo). Das Resultat war der Aufstieg Japans zur Wirtschaftsmacht, vom Billiganbieter zum High-Tech- und High-Quality-Land. Einer der wichtigsten Adepten: Taiichi Ohno von Toyota, der das System zum Toyota Management System perfektionierte. Wesentliche Teile von Lean gehen auf TMS zurück - daher enthält Lean auch viele japanische Begriffe.
Zentral für Lean ist die Delegation von Zuständigkeit und Verantwortung auf die Arbeitsebene für die Optimierung der eigenen Arbeit auf dem "shop floor" und in den Büros. Lean umfaßt einen entsprechenden Werkzeug satz. Es gilt Verschwendung ("muda") zu vermeiden in den Bereichen:
Überproduktion | z. B. durch Optimierung der Rüstzeiten ("SMED") und Erhöhung der Anlagenverfügbarkeiten. |
Wartezeit | z. B. durch Pullsysteme (Kanban) - "Value Stream Mapping". |
überflüssiger Transport | z. B. durch geeignete Anordnung der einzelnen Arbeitspunkte |
ungünstiger Herstellprozess | Im Kontext von Lean geht es um möglichst einfache Handgriffe - im größeren Kontext kann dies eine Quelle für Six Sigma Projekte sein. |
überhöhte Lagerhaltung | z. B. relativ hohe Zwischenproduktlager (siehe Theory of Constraints), Kanban-Ansätze - beeinflußt aber auch von Rüstzeiten für Produktumstellungen |
unnötige Wege | z. B. Optimierung von Kontrollgängen ("Spaghetti-Plot") |
Herstellung fehlerhafter Teile | machen Nacharbeit erforderlich. Optimierung auf der Basis der täglichen Erfahrungen. |
Ziel ist es, den Anteil nicht-wertschöpfender Tätigkeiten zu minimieren - dazu bedient man sich z. B. der Wertstrom-Analyse ("Value Stream Mapping"):
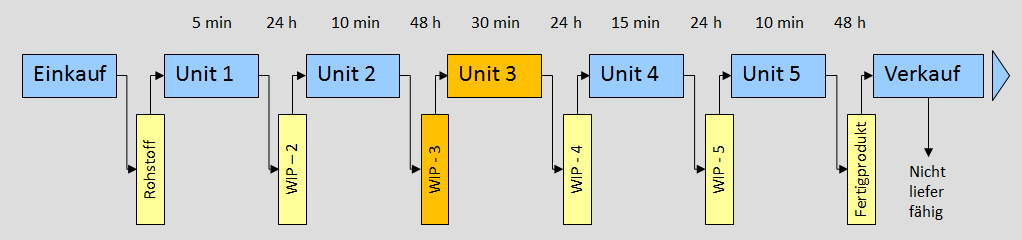
Die Value Stream Map ist imgrunde eine Process Map ergänzt um Bearbeitungs-, Transport-, Wartezeiten, oftmals ergänzt um Angaben zur Kapazität der einzelnen Einheiten, detailliertere Daten zu og. Zeiten (kürzeste, längste, Verteilung) - und ergänzt um die Steuerungsmechanismen für die Wertschöpfungskette. Je nach vorhandenem Datenbestand läßt sich eine VSM als Grundlage für Simulationen nutzen.
Sauberkeit und Ordnung ("5S") spielen eine wichtige Rolle bei der Vermeidung von Totzeiten, aber auch im Bereich der Arbeitssicherheit.
Lean ist typischer Bestandteil eines KVP-Systems, bei dem die inkrementelle Verbesserung im Mittelpunkt durch die Mitarbeiter vor Ort steht. Entsprechend handelt es sich um einen inkrementellen Verbesserungszyklus: PDCA (plan–do–check–act/adjust, "Deming-Zyklus").
Rüstzeitenoptimierung - SMED
SMED (Single Minute Exchange of Dye) steht für den raschen Wechsel von Spritzgußformen, um dem wachsenden Bedarf nach kundenspezifischen Lösungen, kleinen Losgrößen und geringem Working Capital zu begegnen. Ein Beispiel bieten die Rennställe der Formel 1, die Reifenwechsel in einer beeindruckenden Geschwindigkeit hinbekommen ...
Entsprechendes gilt natürlich auch für Reparaturmaßnahmen, deren punktgenaue Einplanung und downtime-optimierte Durchführung (wenn Kapazität der Engpaß ist) bzw. der ressourcen-optimierte Durchführung (wenn Kostenaspekte im Vordergrund stehen) --> siehe Throughput-Accounting unter TOC.